Tape Looms
“Just arrived, and to be Sold Cheap, a Choice variety of Haberdashery, …Laces, Cadisis (type of woolen tape), Quality’s Tapes, Pins, Needles, Shirt-button, Crewels in Shades.”
Boston News-Letter, Apr 15/22, 1736
Tape looms are used to weave narrow, sturdy tapes. Usually not more than an inch wide, and they were woven narrower, tapes were colorful and were an important part of every household. Today where we use buttons, zipper, Velcro and snaps, the Colonial ladies used buttons, pins and tapes.
Although available ready-made from merchants, the tape loom provided an easy method to produce tape at home. Two typical styles of tape looms are the focus of this article. The simplest was a thin board fashioned with small drilled holes and slots.
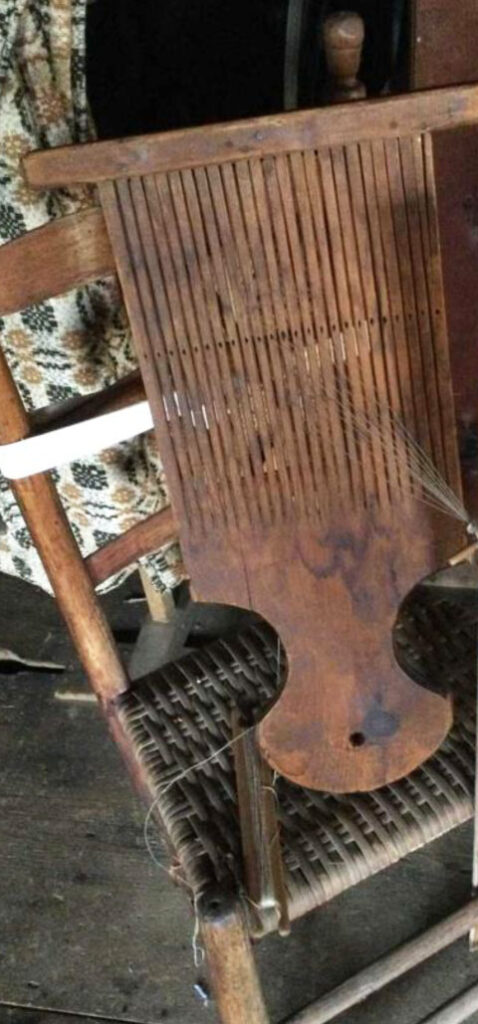
This type of tape loom was made in a variety of styles often dictated by the creativity of the maker. In studying originals, there is no indication that there was a standard measure for height and width. The loom pictured here is not fully set-up. When prepared for weaving, the weaver deciding on the number of threads needed, there would be a thread for each small hole and slot in the required width.
Terms used in reference to cloth weaving looms applied to the little tape loom as well. The long threads, going from the back to front of the loom are the warp; the threads passing over and under the warp threads (the crosswise threads) are called the weft or woof. A shuttle is used to hold the weft thread for ease in passing it through the shed – the shed is the opening formed when the warp threads are separated.
It is the set-up of the small holes and slots that allows the weaver to separate the warp threads and create the shed. The threads in the holes do not move, only the warp threads in the slots, therefore: when the weaver, holding the warp thread ends in her/his hand brings the warp threads down, toward the base of the loom, one shed is formed, after passing the weft through, the weaver brings the warp threads up, higher than the threads held in the small holes and that creates a second shed. This up and down method reverses the position of the warp threads, so that they interlock with the weft thread. The tape formed by this type of weaving method is called warp face because one only sees the warp threads and not the crossing of the weft threads.
The second style of loom discussed in this article is the box tape loom. In terms of weaving the process is the same. The advantage of the box loom is that it is designed with a beam in the back which allows the weaver to wind up the length of the warp, which might be several yards. The winding of the warp threads on the beam allows for better control over the tension on the warp threads, then might happen when the warp ends are tied to a bed post.
In some box tape looms a small beam was also added at the front of the loom itself, offering the weaver a place to wind up tape as it is being woven. Both the back warp beam and the front cloth beam would have a ratchet gear for them on the outside of the box to apply tension.
Tapes were most often woven in linen, cotton or wool threads (silk was used for ribbons). Once woven they had numerous uses, the following offers some examples: as apron strings, binding at the waist edge of an apron and petticoats; garters used by men, women and children for their stockings; used as ties at the knees of men’s breeches, as well as lacing for the gusset sewn at the back waist of men’s breeches; used as drawstrings for ladies’ and children’s shifts (arm and neck openings); tapes were used to tie cloth bags used for storage of all sorts of supplies; colorful tapes were also used as decoration on clothing.
Knowing that tape loom weaving produces a warp face piece, the weaver would set the pattern with these threads. The most common pattern for a tape is stripes. In order to get a solid stripe at least two threads of the color must be threaded next to each other. If this is not done and one thread is left “alone” it will form a dot of color in the piece. This single, colored warp thread will only be on top of every other shot, therefore unless there are two of them, the single thread will only show its color every other pass of the weft thread. Knowing these two principles the weaver could vary the color pattern despite the limitations of the tape loom.
Louise Miller, LCHA Education Director